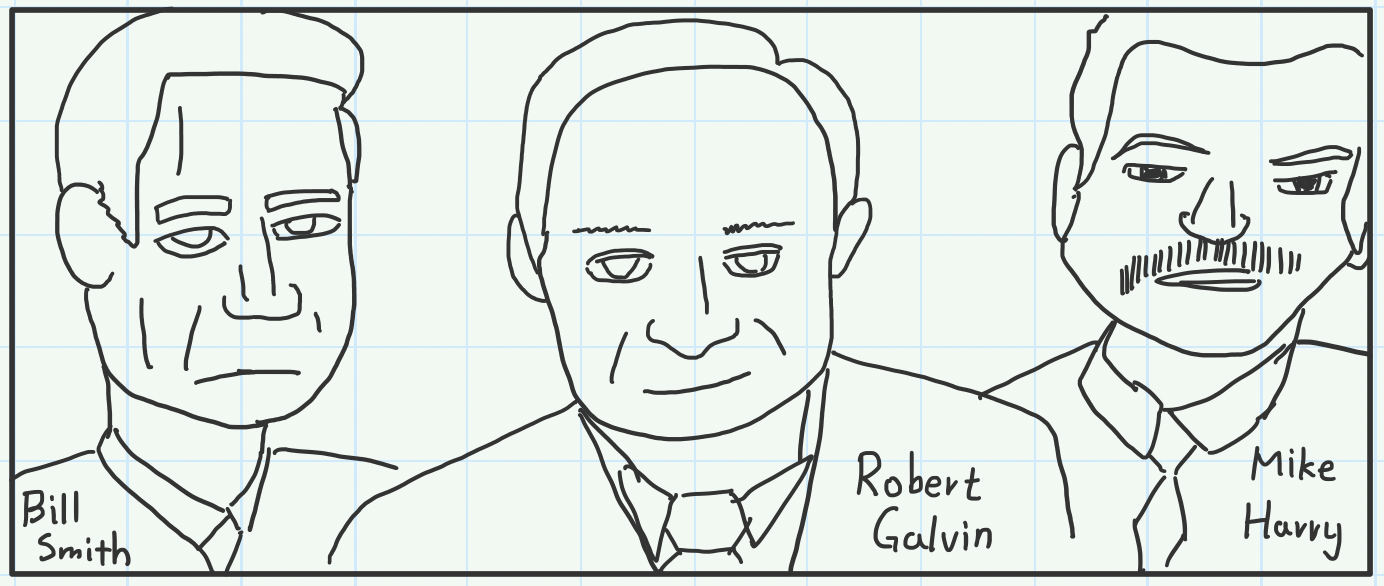
1. Six sigma
6번째 포스팅은 식스시그마(6 Sigma, Six sigma)
입니다. 이전 포스팅 에서 잠깐 통계적 이해
를 돕기위해서 6 Sigma
를 언급한 적이 있습니다. 원리와 접근방법은 동일하나, 6 Sigma
가 Quality
, Management
의 측면에서는 어떻게 이용되는 지를 얘기합니다. 그리고 6 Sigma
로만 논문을 쓰고 박사가 되기도 합니다. 그만큼 파고들수록 어려운 학문이기에 이 포스팅을 읽고나서 흥미가 생기신다면, 보다 전문적인 학술탐구를 해보시길 권장드립니다.
1.1. Industrial Revolution
**언제부터 삶이 편해지기 시작했을까? **
1969년, 컴퓨터의 보급으로 3차 산업혁명을 알립니다. 그리고 하드웨어가 더 발전하며 21세기 초부터는 4차 산업혁명이 시작됐다고 하죠. 모든 산업의 동향이 급격하게 바뀐 것은 사실입니다. 그러니 어떤 키워드
에 집중됐는 지 확인해봅시다. 1차 산업혁명
은 증기기관
, 에너지원의 혁명
이라고 할 수 있구요. 2차 산업혁명
은 양산
, 제품생산의 혁명
입니다. 3차 산업혁명
은 전자기술, 자동화
, 인터넷 혁명
입니다. 지금의 4차 산업혁명
은 지능화, 가상화
, 모빌리티의 혁명
이라고 볼 수 있죠. 저장소도, 서버도, 컴퓨터도, 운전사, 심지어 화폐까지 모두 고도의 가상으로 존재하며 고도의 지능으로 편의를 제공하고자 합니다.
역사에 따르면, 실제 일상
에서 산업혁명
을 바로 느낄 수 있었습니다. 그렇다면, 우리는 언제 4차 산업혁명
을 느낄 수 있었을까요? 제 개인적인 주관이지만, 모두 공감할 것이라 생각합니다. 스마트폰
의 시작이라고 생각합니다. 핸드폰이 단순 이동통신전화기에서 이동통신컴퓨터로 바뀌어 많은 삶을 바꾸어 놓았죠. 또한 스마트폰의 사용으로 데이터 사용량이 폭증하고 여러 데이터 수집이 원활해졌으며 이는 지능화
에 큰 도움을 줬습니다.
1.2. Motorola
1980년대, 그런 스마트폰
의 전신인 이동통신전화기인 핸드폰
과 관련하여 미국
과 일본
에서의 반도체 전쟁의 시대
가 시작됩니다. 일본
이 세계시장에서 강세였고 그 중에서 Motorola
가 일본 내부에서도 우세를 선점하기위해 품질개선
에 집중합니다.
5년안에 10배의 품질개선을 달성한다 - Robert Galvin
Motorola
회장이 10배의 품질개선을 하라고 선언했습니다. 직원들 난리났죠? 그 중에 현장 엔지니어, Bill Smith
의 연구결과가 있습니다.
- 결함에 의해 재작업을 거친 결과물은 고객의 초기사용단계에서 고장이 잦습니다.
- 다른 메이저 기업들의 현장을 살펴본 결과, 애초에 수리 및 재작업에 필요없는 수준으로 생산합니다.
지금보면 당연한 얘기가 맞긴한데, 이 시대에 본격적으로 머리에서 이미 인지한 내용을 Motorola
가 충분한 연구와 분석을 통해 정리한 것입니다. 여기서 본격적인 누적수율(Rolled Throughput Yield)과 숨은 공장(Hidden Factory) 의 개념이 나옵니다. 그리고 Mikel Harry
가 들어오죠.
” 저 얘기대로 한다면, 누군가 불량기준을 널널하게 잡을 것이다. 그러니 체계적인 방법론을 만들고 전략을 수립한다 - Mikel Harry”
6 Sigma
가 시작됩니다,
1.2.1. Bill Smith’s A/S report
Bill smith
는 단위당 결함 총계
이 증가할수록 생산의 적폐요소들이 늘어난다고 얘기합니다. 그러니 단위당 결함 총계
를 줄이면 고객에게 운송된 결함과 제품 수명 초기 불량률, 싸이클 타임이 감소되며 결론적으로 제조비용도 감소되고 고객도 만족하고 A/S 비용도 감소하는 모두가 행복한 세상이 찾아옵니다.
1.2.2. Result
그래서 이를 적극적으로 진행한 결과를 말씀드리면 시작 1년째인 1988년
에 480만 달러가 절약되구요. 4년째인 1991
년에는 22억 달러가 절약됩니다.
1.3. What is 6 sigma
6 Sigma
를 아직도 쓰는 곳이 있냐고 물어보는 사람 제법 있습니다. 시간이 지나며 많은 품질개선
에 대한 연구가 이뤄져 다른 대안이 많이 생겼습니다. 경영진 측에서는 좋은 일이죠. 그럼에도 불구하고 학계에서는 6 Sigma
를 꼭 알려줍니다. 여러가지 이유 중에서 두 개만 딱 정해서 말해보자면 최근에 생긴 대안들이 Six sigma로부터 나온 것이 많습니다
그리고 여러분이 새로운 방법론을 생각할 때 Six sigma가 도움됩니다.
로 정할 수 있습니다. 그러니 경영과 공학의 관점에서 Six sigma
를 알아봅시다.
1.3.1. Definition in terms of business
요소 | 정의 | 비고 |
---|---|---|
품질지표 | 통계적 의미로는 100만 개중에 3.4개의 결함을 의미 | 시그마 측정은 제품 및 서비스를 만드는 과정상의 상태를 측정하는 척도 |
개선 프로세스 및 기법 | 전 비지니스 시스템에 걸쳐 통계 수법을 일련의 프로세스로 조합한 패키지 툴 | DMAIC 개선방법 |
사업 전략 | 전사적 차원에서 경영혁신을 달성하는 전략 | 프로세스 측정 -> 현위치 파악 -> 목표 설정 -> 전사적 활동 -> 성과측정 |
생활 철학 | 우리가 하는 모든 실수를 줄여 Loss 를 제거 | 현명한 일이란 로스와 낭비를 줄이고 집중하는 업무로 효율적인 작업을 의미 |
1.3.2. Definition in terms of engineering
공학적인 측면에서 Target
과 USL or LSL
의 거리를 얼마로 정할 건지가 관건이었습니다. Mikel Harry
는 1.5 sigma
를 얘기했습니다만, 아래를 보며 얘기하겠습니다.
k | PPM | k | PPM |
---|---|---|---|
6 | 0.02 | 6 | 3.4 |
5 | 0.5733 | 5 | 233 |
4 | 63.34 | 4 | 6,210 |
3 | 2700 | 3 | 66,807 |
2 | 45500 | 2 | 308,537 |
k
는 target
으로부터 제한선
의 거리를 볼때, 1.5sigma
로 잡으면 양측 3sigma
라고 볼 수 있죠. Mikel Harry
가 생각한 기준인데요. 이에 대한 근거를 설명드리겠습니다. 주제만 말씀드리면 선험적인 이유인데요. 제조현장에서는 단기와 장기의 산포는 다릅니다. 개선방향을 파악할때는 현재 공정에서 바로 할 수 있는 것은 단기 산포를 보고 개선을 시도합니다. 그리고 시간에 따라 단기에 대한 Z score는 장기쪽으로 움직이게 되는데 이 차이가 대략 1.5sigma
인 것을 실험적으로 확인할 수 있었습니다.
참고로 알아두시면 좋은 내용인데요. 1.5 sigma
를 정하는 Mikel Harry
의 주장은 본격적으로 잘못됐다고 얘기하는 분들이 상당히 많습니다. 여기서는 해당 내용을 다루지 않을 것이지만, 따로 알아보시면 좋습니다. 저도 왜 잘못됐는지 알아보다 많은 것을 깨달았죠.
2.1. How does it work?
2.1.1. Short/Long Term sigma level
Long Term Performace
는 장기로 들어가며 당연하게도 전체 Data를 산출합니다. Short Term Capability
는 장기중에서도 좋은 샘플로만 골라서 공정이 얼마나 좋을 수 있는지를 따져봅니다. 기준은 총 세가지가 되죠.
- 최소의 산포를 갖는 기간으로
- 최대의 성능을 갖는 기간으로
- 최대의 성능을 갖는 범주로
2. Concept / Goal / Purpose
본론에 들어와서, 6 Sigma
에 대한 개념을 잡았으니 이를 통해 어떻게 활용할 수 있을 지 시야를 넓히겠습니다. 위에서는 원리에 대한 이해였다면, 시스템에 대한 이해를 목적에 두고 설명하겠습니다.
2.1. Feature finder without noise
Response | Predictors |
---|---|
Y | X1 … Xn |
종속 | 독립 |
결과 | 입력, 프로세스 |
효과 | 원인 |
증상 | 문제 |
기록 | 관리 |
특징-프로세스 중심으로 Rsponse
인 Y에 대해서 연구하고 개선하는 것이 아닙니다. 주요 X들을 발견하고 관리하여 원인을 제거해서 결론적으로 결과가 바로 나아지도록 원인해결에 활동을 합니다. 그러나 원인인자인 X에 대한 Noise
를 고려안하는 것이 6 sigma
의 제일 아쉬운 점입니다.
2.2.COPQ(Cost Of Pool Quality)
COPQ
는 저품질 비용으로 평가/검사 비용, 내부실패 비용, 외부실패 비용을 포괄하여 얘기합니다. 보여지는 외부실패 비용보다 내부 실패비용이 훨씬 많으며 이 내용은 다음 포스팅에 이어서 설명하겠습니다. 마무리하며 COPQ
측정이 비용 해결과 반드시 직결되는 것은 아니며 구체적인 행동 대안이 없는 경우도 있습니다. 그리고 부정적인 영향이 보고에 올라올 때 크게 충격을 먹기도 하구요. COPQ에 집중한 나머지 다른 중요한 비용을 놓칠 수 있으며 애초에 COPQ가 부정확할 수 있습니다.
그럼에도 불구하고 COPQ
분석의 필요성은 계속 대두됩니다. 왜냐하면 분석활동에서 Hidden Factory
가 노출됩니다. 그리고 지속적인 측정활동으로 시스템을 계량적으로 볼 수 있는 변화가 생깁니다. 문제의 우선순위를 정렬할 수 있구요. 이러한 활동을 통해 조직원들의 동기부여 또한 이뤄집니다. 그리고 본질적으로 잘 측정된 COPQ
를 절감한다면 기업의 이윤 증대의 지름길이기 때문입니다.